whatever AC drive you pick should be from a supplier who is as LOCAL as possible and can support you when things are not going as planned. Most use the same or similar technology (otherwise they would not survive in the market) and every drive works great when you commission them, until it doesn't. That's when the value of a good local supplier arises.
If the ABB filter produces 10% voltage drop at the motor, it means that the filter reactor is around 16% impedance (10%Voltage Drop/60% reactive current=16% reactance) which is to me excessive. This will create a slugish speed control, going up and down around the operating speed.
On paper its the 1:N term... In practice the differences are massive because of snubbers, control, isolation, etc....
Do the basic math on both. You'll see advantages on both sides of the design on paper which aren't too many, but as other people have stated here... You need to define your spec a little better so that we can help because they are two very different switchers which solve two very different problems.
Do the basic math on both. You'll see advantages on both sides of the design on paper which aren't too many, but as other people have stated here... You need to define your spec a little better so that we can help because they are two very different switchers which solve two very different problems.
On the delta side you use the term BEF but I would still simply call it REF - the "B" doesn't necessarily indicate a differential type protection as there are other instances where unrestricted earth fault protection is used as back up in the hope that something else would operate first. If there is an ef on the TF delta, the REF would be considered as the principle, not back up, protection (in the absence of TF diff 87T)
A)- Rating equal 150% of the primary current (under no circumstances to be more than 300% - this is exceptional if the adopted secondary fuse rating at LV not exceeding 125% of the secondary full load current).
B)- Compliance to particular conditions related to protection of secondary side.
B)- Compliance to particular conditions related to protection of secondary side.
No matter what level of voltage you are dealing with, the ground wall insulation will be heavier than the conductor insulation. Potential to the ground wall is line voltage. Turn to turn voltage, especially in a medium or high voltage machine in minimal in comparison to the line voltage. The coils for medium and high voltage machines are made with the turns in a perfect stack unlike a random wound coil where it is very possible that the first turn of a coil can make contact with the last turn of a coil.. The turns of one coil can make contact with the turns of another coil.
It is absolutely impossible for a utility to change the phase sequence. Why? Because the utility is connected to the local grid, the local grid to the regional grid, the regional grid to the national grid, and the national grid to the international grid. So, unless you don't change the phase sequence in the entire network you cannot change it locally.
The motor I need to stop is a 90W Single Phase Permanent Capacitor Induction motor, run straight from 230V AC mains. I'm not able to use a variable speed drive, separate DC injection braking unit or a DC electromagnetic brake. So I was considering DC dynamic braking, by applying DC voltage across the windings once mains power is removed.
The application was the addition of colours and flavours to a confectionary product and the required flow rates were very low. It was felt that a series of flow transmitters was an expensive and over-the-top solution, yet accuracies asked for and shifting conditions meant that simply setting the dosing pumps at a set rate was not adequate.
We know that the phase sequence is one of many conditions of the synchronization operation, and made in the beginning of construction. But if for any reason we need to check the phase sequence for two different sources of power. How to do that?
Driving the motor with sinusoidal voltages conveniently eliminates the issue of dv/dt related problems, voltage doubling effects and common mode currents flowing into the motor. The motor-side inverter of the variable frequency drive would have an LC-filter, and the capacitor voltage is a controlled sinusoid.
Current trend indicates that EPR cables are the preference over XLPE cables considering all the factors that are being evaluated. One very significant issue where EPR becomes more advantageous is on the issue of after installation "proof testing" of the cable. While EPR cables can take either a DC high pot testing procedure or AC High pot testing procedure, installation of XLPE cables do not guarantee / recommend a DC High pot testing on their cables.
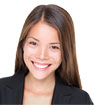
Hot Tags
Featured
Frequency directly represents no of rotation of rotor for that machine,
the higher the frequency the more the rotation of the rotor, i.e. the
rpm of the motor there by result ...
Due to power electronics technology and microelectronics technology rapid development, variable frequency drive reforms and upgrades speed also is faster, introduce new products, ...
Since the 21st century, China variable frequency drive industry is highly fission. Many foreign brands begin to set up factories in China, the implementation of the localization ...
My personal preference is for an AC line reactor simply because it does a better job of protecting the variable frequency drive from the line and the line from the drive. I've ...
As nowadays there is a trend in green energy production and energy efficiency, what solutions/applications would you recommend in reduction consumed energy of a motor driven by ...
What's New
What are the effects for a 50Hz motor running on 60Hz?
Variable Frequency Drive versus Soft Starter in Harmonics
Considerations in choosing large Variable Frequency Drive
Common Mode Noise Impact in AC drive Applications
AC drives in pumps for energy saving
HMI and SCADA system
Something need to be considered in buying AC drives
ABB sine wave filter
Variable Frequency Drive versus Soft Starter in Harmonics
Considerations in choosing large Variable Frequency Drive
Common Mode Noise Impact in AC drive Applications
AC drives in pumps for energy saving
HMI and SCADA system
Something need to be considered in buying AC drives
ABB sine wave filter