Home » Blog
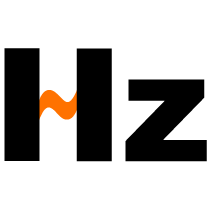
The rated operating voltage must be the same, the motor power will reduced by 50/60 Hz. so if the motor working at the full load, load must be reduced by the same ratio, to keep the motor temperature within the rated limit.
Torque/speed curve is on blower flux. You must reduce load or increase voltage, being careful of insulation voltage level. If motor is fed by variable frequency drive, speed reference must be changed to ensure correct V/Hz control (open loop control).
Variable Frequency Drives (VFD) that do not have either an AC line reactor or a DC bus choke, will typically exhibit a THDi greater than 85% at all loading conditions. The THDi is dependent on the conduction angles of the rectifier. Any inductive reactance in the supply, plus the overall impedance will reduce the peak charging current to the capacitors and increase the conduction angle and reduce the THDi.
So VFDs with standard 6 pulse rectifiers will produce harmonic currents in the supply ranging from around 38% to 100% depending on the load and the reactance in the circuit. VFD with active front end can have a reduced harmonic current down to around 5% provided that the active front end is optimised for harmonics rather than regeneration. These harmonic currents are drawn from the supply the whole time the variable frequency drive is operating.
So VFDs with standard 6 pulse rectifiers will produce harmonic currents in the supply ranging from around 38% to 100% depending on the load and the reactance in the circuit. VFD with active front end can have a reduced harmonic current down to around 5% provided that the active front end is optimised for harmonics rather than regeneration. These harmonic currents are drawn from the supply the whole time the variable frequency drive is operating.
Advances in high-speed electric motor technology along with improvements in the cost and the performance of VFD (variable frequency drive) systems make direct coupling of a gearless electrical motor to a pump worth considering for many services requiring large VFDs. Brushless synchronous motors with two-pole rotors often suit high performance duties. Special applications may benefit from other options such as induction electric motors.
Radiated noise from an AC drive cable is a source of interference with adjacent systems that is often easier to identify and rectify than common mode noise. In the latter, high levels of noise across a broad frequency range, often from 60 Hz to 30 MHz, can capacitatively couple from the windings of the motor to the motor frame, and then to ground.
AC drives are designed to provide variable speed control. They maintain the optimal speed required for an application to enhance production and save energy. Low- and medium-voltage drives gradually accelerate and decelerate motors and pumps, helping protect mechanical components and extend their life, while reducing inrush currents, which helps save energy. AC drives are used in a broad range of industries and applications—including HVAC, water and wastewater, and oil and gas.
HMI stands for Human Machine Interface and HMI is a term and not an application.
HMI is the communication/interaction layer between the user and the process.
In the process industry the "Human" is the operator and the "Machine" is the process control data and instruments. HMI is not a term exclusively used for processes but you can find the HMI in any system.
whatever AC drive you pick should be from a supplier who is as LOCAL as possible and can support you when things are not going as planned. Most use the same or similar technology (otherwise they would not survive in the market) and every drive works great when you commission them, until it doesn't. That's when the value of a good local supplier arises.
If the ABB filter produces 10% voltage drop at the motor, it means that the filter reactor is around 16% impedance (10%Voltage Drop/60% reactive current=16% reactance) which is to me excessive. This will create a slugish speed control, going up and down around the operating speed.
I have been involved in the design for production of many power electronic products, including switching power supplies, electronic ballasts and automotive electronics for Hybrid vehicles. What I have found is the consistency of the breakdown voltages is different for AC and DC. I've sampled 100 ballast from a high volume production line. 50 of the units were subjected to a slow ramp to a sufficiently high DC Hipot breakdown voltage. The other 50 units were subjected to the same ramp but with AC.
Bridges are very common in Hi-Reli applications such as aircraft and almost necessary for inverters and variable frequency drives. I'm curious to hear which type of industry exhibited these "recent rumblings" about using bridges. As a contractor I have a good opportunity to witness a lot of problems with all types of topologies. Problems such as this or that transistor getting too hot are secondary; The main problem I ALWAYS see is that a worst case analysis was not performed for extreme conditions.
On paper its the 1:N term... In practice the differences are massive because of snubbers, control, isolation, etc....
Do the basic math on both. You'll see advantages on both sides of the design on paper which aren't too many, but as other people have stated here... You need to define your spec a little better so that we can help because they are two very different switchers which solve two very different problems.
Do the basic math on both. You'll see advantages on both sides of the design on paper which aren't too many, but as other people have stated here... You need to define your spec a little better so that we can help because they are two very different switchers which solve two very different problems.
On the delta side you use the term BEF but I would still simply call it REF - the "B" doesn't necessarily indicate a differential type protection as there are other instances where unrestricted earth fault protection is used as back up in the hope that something else would operate first. If there is an ef on the TF delta, the REF would be considered as the principle, not back up, protection (in the absence of TF diff 87T)
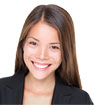
Hot Tags
Featured
Frequency directly represents no of rotation of rotor for that machine,
the higher the frequency the more the rotation of the rotor, i.e. the
rpm of the motor there by result ...
Due to power electronics technology and microelectronics technology rapid development, variable frequency drive reforms and upgrades speed also is faster, introduce new products, ...
Since the 21st century, China variable frequency drive industry is highly fission. Many foreign brands begin to set up factories in China, the implementation of the localization ...
My personal preference is for an AC line reactor simply because it does a better job of protecting the variable frequency drive from the line and the line from the drive. I've ...
As nowadays there is a trend in green energy production and energy efficiency, what solutions/applications would you recommend in reduction consumed energy of a motor driven by ...
What's New
What are the effects for a 50Hz motor running on 60Hz?
Variable Frequency Drive versus Soft Starter in Harmonics
Considerations in choosing large Variable Frequency Drive
Common Mode Noise Impact in AC drive Applications
AC drives in pumps for energy saving
HMI and SCADA system
Something need to be considered in buying AC drives
ABB sine wave filter
Variable Frequency Drive versus Soft Starter in Harmonics
Considerations in choosing large Variable Frequency Drive
Common Mode Noise Impact in AC drive Applications
AC drives in pumps for energy saving
HMI and SCADA system
Something need to be considered in buying AC drives
ABB sine wave filter