Home » Blog » Energy saving » Implement Space Vector PWM FOR PMSM
Implement Space Vector PWM FOR PMSM
There are many ways of implementing SVPWM, it is having the third harmonic sine injected in to sine phase voltages to get better DC bus utilization (15% more).
In practical scenario, the selection of one particular technique is based on many factors.
1. Reduced computation or complexity requirement based on the device you use
2. Reduced switching losses (Edge aligned or centre aligned)
3. Again in Center aligned mode zero switching state (000 or 111) selection for point 2.
etc.
4. With alpha & beta input or magnitude angle input available etc., for point 1.
5. Modulation range
You can implement the same algorithms in different ways depending on what are your overall requirements. Mainly what is the output of your control algorithm (point 4).
For standard 3-ph voltage inverter the best DC-bus utilization that can be achieved (in linear modulation range) is VDCB=Vphase-phase_amplitude => Vphase_ampl = VDCB/sqrt(3), which is about 15% more than VDCB/2 (as for inv. Cl.).
Such utilization can be achieved in infinite number of ways. All is about to add/inject 3rd HARMONIC AND ITS HARMONICS, in the article referenced by Sandro this represented by the ei(t). So ei(t) = sum(A3k*sin(3k*omg*t+fi3k) where k = 1 .. infinity; fi3k is phase shift of the "3k" harmonic; A3k is amplitude of "3k" harmonic; omg is angular speed and t is time. As you see, there is infinite number (Aleph-naught for math purist ;-) ) of possible combinations of amplitudes and phase shifts.
For practical use there are additional notes:
1. Reduced computation or complexity requirement based on the device you use
- honestly, if you having trouble with computational load of the SVM (do not get me wrong, I still support efficient implementations) then you probably using wrong device. Today you find on the market reasonably priced devices which can do such job in about 1us or less. In case such devices are still above your budget then SVM is not your technique, because you probably use very simple control methods (e.g. scalar control) so you can also use very simple sine PWM methods (with 3rd harmonic injection).
2. Reduced switching losses (Edge aligned or centre aligned)
- note all the SVM methods claiming the reduction of the switching losses sacrifice something else - in most cases magnitude of current (or equivalently torque) ripples and/or fundamental frequency/speed range. This is because such techniques reduce number of “switchings”; i.e. number of alternations of the applied space vectors; per certain period, so the (space vector) current is allowed to “grow” in certain direction “longer” than in case of more alternations/switchings are performed within the same time. Therefore if your application (e.g. servo-drive) requires to achieve small current/torque ripples then all SVMs are practically equal for you. Because any SVM technique will produce very similar switching losses when achieving the same current ripples.
Regarding the limited speed range, if your application must work with full torque/current at zero speed then each power switch must be thermally designed for full losses => no real savings.
Reality, of course is a bit more complex, however, for first level guidance the above holds.
4. With alpha & beta input or magnitude angle input available etc.,
- yes, it does not make sense to use e.g. SVM implementation based on alpha, beta if your control algorithm gives magnitude, angle where sine PWM with 3rd harmonic injection can be used.
About the choice of a particular modulation, the SV-PWM (implementation is not important) with symmetrical edges is the most common, and IIRC it can be demonstrated that it provides the lowest current ripple. In few words, SVM uses the nearest vectors (thus it avoids unnecessary, while the centered edges give the shortest maximum application times for each vector (considering 1 off-on and 1 off-on commutation per period).
In practical scenario, the selection of one particular technique is based on many factors.
1. Reduced computation or complexity requirement based on the device you use
2. Reduced switching losses (Edge aligned or centre aligned)
3. Again in Center aligned mode zero switching state (000 or 111) selection for point 2.
etc.
4. With alpha & beta input or magnitude angle input available etc., for point 1.
5. Modulation range
You can implement the same algorithms in different ways depending on what are your overall requirements. Mainly what is the output of your control algorithm (point 4).
For standard 3-ph voltage inverter the best DC-bus utilization that can be achieved (in linear modulation range) is VDCB=Vphase-phase_amplitude => Vphase_ampl = VDCB/sqrt(3), which is about 15% more than VDCB/2 (as for inv. Cl.).
Such utilization can be achieved in infinite number of ways. All is about to add/inject 3rd HARMONIC AND ITS HARMONICS, in the article referenced by Sandro this represented by the ei(t). So ei(t) = sum(A3k*sin(3k*omg*t+fi3k) where k = 1 .. infinity; fi3k is phase shift of the "3k" harmonic; A3k is amplitude of "3k" harmonic; omg is angular speed and t is time. As you see, there is infinite number (Aleph-naught for math purist ;-) ) of possible combinations of amplitudes and phase shifts.
For practical use there are additional notes:
1. Reduced computation or complexity requirement based on the device you use
- honestly, if you having trouble with computational load of the SVM (do not get me wrong, I still support efficient implementations) then you probably using wrong device. Today you find on the market reasonably priced devices which can do such job in about 1us or less. In case such devices are still above your budget then SVM is not your technique, because you probably use very simple control methods (e.g. scalar control) so you can also use very simple sine PWM methods (with 3rd harmonic injection).
2. Reduced switching losses (Edge aligned or centre aligned)
- note all the SVM methods claiming the reduction of the switching losses sacrifice something else - in most cases magnitude of current (or equivalently torque) ripples and/or fundamental frequency/speed range. This is because such techniques reduce number of “switchings”; i.e. number of alternations of the applied space vectors; per certain period, so the (space vector) current is allowed to “grow” in certain direction “longer” than in case of more alternations/switchings are performed within the same time. Therefore if your application (e.g. servo-drive) requires to achieve small current/torque ripples then all SVMs are practically equal for you. Because any SVM technique will produce very similar switching losses when achieving the same current ripples.
Regarding the limited speed range, if your application must work with full torque/current at zero speed then each power switch must be thermally designed for full losses => no real savings.
Reality, of course is a bit more complex, however, for first level guidance the above holds.
4. With alpha & beta input or magnitude angle input available etc.,
- yes, it does not make sense to use e.g. SVM implementation based on alpha, beta if your control algorithm gives magnitude, angle where sine PWM with 3rd harmonic injection can be used.
About the choice of a particular modulation, the SV-PWM (implementation is not important) with symmetrical edges is the most common, and IIRC it can be demonstrated that it provides the lowest current ripple. In few words, SVM uses the nearest vectors (thus it avoids unnecessary, while the centered edges give the shortest maximum application times for each vector (considering 1 off-on and 1 off-on commutation per period).
You may also like:
Current trend indicates that EPR cables are the preference over XLPE cables considering all the factors that are being evaluated. One very significant issue where EPR becomes more advantageous is on the issue ...
Since the 21st century, China variable frequency drive industry is highly fission. Many foreign brands begin to set up factories in China, the implementation of the localization of business. See Appendix major ...
The question is about we have an unbalanced system under study and i found that power factor calculation does not obeys the well known geometrical relationship called power triangle nor the arithmetical ...
Advances in high-speed electric motor technology along with improvements in the cost and the performance of VFD (variable frequency drive) systems make direct coupling of a gearless electrical motor to a pump ...
Bridges are very common in Hi-Reli applications such as aircraft and almost necessary for inverters and variable frequency drives. I'm curious to hear which type of industry exhibited these "recent rumblings" ...
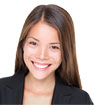
Hot Tags
Featured
Frequency directly represents no of rotation of rotor for that machine,
the higher the frequency the more the rotation of the rotor, i.e. the
rpm of the motor there by result ...
Due to power electronics technology and microelectronics technology rapid development, variable frequency drive reforms and upgrades speed also is faster, introduce new products, ...
Since the 21st century, China variable frequency drive industry is highly fission. Many foreign brands begin to set up factories in China, the implementation of the localization ...
My personal preference is for an AC line reactor simply because it does a better job of protecting the variable frequency drive from the line and the line from the drive. I've ...
As nowadays there is a trend in green energy production and energy efficiency, what solutions/applications would you recommend in reduction consumed energy of a motor driven by ...
What's New
What are the effects for a 50Hz motor running on 60Hz?
Variable Frequency Drive versus Soft Starter in Harmonics
Considerations in choosing large Variable Frequency Drive
Common Mode Noise Impact in AC drive Applications
AC drives in pumps for energy saving
HMI and SCADA system
Something need to be considered in buying AC drives
ABB sine wave filter
Variable Frequency Drive versus Soft Starter in Harmonics
Considerations in choosing large Variable Frequency Drive
Common Mode Noise Impact in AC drive Applications
AC drives in pumps for energy saving
HMI and SCADA system
Something need to be considered in buying AC drives
ABB sine wave filter